Zuverlässigkeits-
MANAGEMENT
Beim Institut für Qualitäts-und Zuverlässigkeitsmanagement, kurz IQZ.
Zuverlässigkeitsmanagement -
Eine Kurzeinführung
Wie leiten Sie Zuverlässigkeitsziele und Lasten für Ihr neues Produkt ab? Wie erproben Sie Kosten-Nutzen optimal? Wie können Sie aus Vorgängerprodukten lernen?
Diese und zahlreiche weitere Fragestellungen lassen sich mit Prozessen und Methoden des Zuverlässigkeitsmanagements beantworten.
Sie sehen gerade einen Platzhalterinhalt von YouTube. Um auf den eigentlichen Inhalt zuzugreifen, klicken Sie auf die Schaltfläche unten. Bitte beachten Sie, dass dabei Daten an Drittanbieter weitergegeben werden.
Mehr Informationen
Wir helfen Ihnen dabei, die richtigen Fragen zu stellen und diese dann kompetent zu beantworten. Dabei entwickeln wir mit Ihnen die zu Ihrem Unternehmen passenden Prozesse, erarbeiten mit Ihnen Schulungskonzepte und helfen Ihnen bei der Implementierung notwendiger Methoden. Falls gewünscht, programmieren wir Ihnen auch die entsprechende Spezialsoftware, um z.B. eine Erprobungsplanung teilautomatisiert zu erstellen oder Felddaten auszuwerten. Den Grad der Unterstützung bestimmen natürlich Sie!
Kurzum: Wir sind Ihr kompetenter Partner für ein ganzheitliches Zuverlässigkeitsmanagement.
Unsere
Leistungen
- „Hardness Check Product liability“
- Projektunterstützung (Lastableitung, Use-Cases, Zieldefinition, Erprobungsplanung, Zuverlässigkeitsprognose, Zuverlässigkeitswachstum, Risikobewertung mittels geeigneter Methoden, Garantiekostenabschätzung)
- Aufbau von notwendigen Prozessen und Arbeitsanweisungen
- Projektunterstützung (Lastableitung, Use-Cases, Zieldefinition, Erprobungsplanung, Zuverlässigkeitsprognose, Zuverlässigkeitswachstum, Risikobewertung mittels geeigneter Methoden, Garantiekostenabschätzung)
Zuverlässigkeitsmanagement
Zuverlässigkeitsmanagement (Reliability Management) bedeutet zu einem frühen Zeitpunkt im Produktentstehungsprozess Zuverlässigkeitsvorgaben zu definieren und deren Entwicklung im Sinne eines Zuverlässigkeitswachstums (Reliability Growth) über den gesamten Produktentstehungsprozess zu überwachen. Aber Zuverlässigkeitsmanagement hört nicht nach dem Serienstart auf. Auch während des Feldeinsatzes werden moderne Methoden der Felddatenauswertung und Mustererkennungsverfahren genutzt, um zum einen eine passive Marktbeobachtung durchzuführen und zum anderen aber auch wichtigen Input für neue Entwicklungsprojekte zu generieren.
Wichtig dabei ist, dass Zuverlässigkeit in die Unternehmenskultur einfließt und kein einmaliges Ereignis ist. Eine organisatorische und prozessuale Verankerung im Unternehmen ist folglich unverzichtbar. Zahlreiche Standards und Richtlinien, wie z.B. VDI 4004, DIN 60300 oder VDA 3.1 und 3.2, beschäftigen sich mit dem Themenkomplex Zuverlässigkeit und werden durch unsere Experten beherrscht.
Wie bereits erwähnt, kann Zuverlässigkeitsmanagement in einen präventiven sowie in einen reaktiven Bereich unterteilt werden. Beide Bereiche sind eng miteinander verzahnt, tauschen im Optimalfall Informationen aus und stellen eine ganzheitliche Betrachtungsweise des Zuverlässigkeitsmanagements sicher. Präventives und reaktives Zuverlässigkeitsmanagement werden im Folgenden näher beschrieben.
Präventives Zuverlässigkeitsmanagement
Präventives Zuverlässigkeitsmanagement beschäftigt sich mit den Fragen der Zuverlässigkeit während des Produktentstehungsprozesses (PEP), um schon zu einem frühen Zeitpunkt potentielle Fehler zu entdecken und kostengünstig abzustellen. Ziel ist es, ein hoch zuverlässiges und sicheres Produkt zu entwerfen, welches sich durch minimale Feldausfälle und damit einhergehend geringe Garantie- und Gewährleistungskosten auszeichnet. Dies ist besonders im Hinblick auf steigende Gewährleistungszeiten extrem wichtig. Zudem soll das Zuverlässigkeitswachstum sichergestellt werden.
Folgende Themen sollten in einem präventiven Zuverlässigkeitsmanagement behandelt werden:
- Zuverlässigkeitsanforderungen und -ziele (Erfahrungswerte, Wettbewerbsdaten, normative Anforderungen, Kundenanforderungen, etc.)
- Zuverlässigkeitsspezifikationen (u.a. Test- und Prüfplanung, Lastenheft für Lieferanten, Bewertung Systemaufbau)
- Zuverlässigkeitsvorhersage und Beurteilung (u.a. Entwicklungstests, Systemmodelle, Simulationen)
- Zuverlässigkeitsnachweis (Prototypentest)
- Zuverlässigkeitsprüfung (Vorserientest)
- IST-Aufnahme Zuverlässigkeit (Fertigungstests, Felddatenanalyse àreaktive Methoden)
In der nachfolgenden Abbildung ist ein ganzheitlicher Zuverlässigkeitsprozess abgebildet, wie er durch die Mitarbeiter des IQZ schon bei namhaften Unternehmen umgesetzt wurde.
Folgende Methoden werden von uns im präventiven Zuverlässigkeitsmanagement angewandt:
- FMEA
- FMECA
- RBD
- FBA/FTA (Prototypentest)
- Markov-Modelle
- WeiBayes
- MTTF/MTBF
- Success-Run,
- Sudden Death
- EOL-Test
- Raffungsverfahren
- Lastableitungen
- Zuverlässigkeitspartitionierung
- Simulation
- Mathematische Optimierung
- Zuverlässigkeitsblockschaltbilder/Redundanzanalyse
- Sicherheitsnachweis
- Risikobewertung
Reaktives Zuverlässigkeitsmanagement:
Das reaktive Zuverlässigkeitsmanagement betrifft sämtliche Lebensabschnitte des Produktlebenszyklus, welche nach Auslieferung des Produkts an den Kunden erfolgen. Dabei wird versucht, anhand realer Daten aus dem Feld eine Aussage zur Zuverlässigkeit des entsprechenden Produkts zu treffen. Zudem gibt es Methoden, mit deren Hilfe sich aus Daten Fehlerschwerpunkte ermitteln lassen (Mustererkennung). Diese Methoden sollten zu Beginn einer Zuverlässigkeitsanalyse von Felddaten immer vorgeschaltet werden, um den späteren Analyseaufwand aufkritische Problemfälle zu fokussieren. Somit werden finanzielle oder auch personelle Kapazitäten nicht nach dem Gießkannenprinzip auf alle Produkte gleichmäßig, sondern zielgerichtet verteilt.
Die Ergebnisse aus Felddatenanalysen – z.B. aus einer Zuverlässigkeitsprognose – eignen sich hervorragend zur Unterstützung des präventiven Zuverlässigkeitsmanagements. Unter anderem lassen sich damit Zuverlässigkeitsanforderungen und folglich Ziele formulieren, die eine wichtige Grundlage im Entwicklungsprozess darstellen. Weiterhin sind Felddatenanalysen ein geeignetes Mittel zur Unterstützung im Garantie- und Gewährleistungsmanagement. Mit ihrer Hilfe lassen sich Garantiekosten prognostizieren, Risiken bei Garantiezeiterweiterungen abschätzen oder Rückrufaktionen verifizieren. Auch bei einer bevorstehenden Serienschadenverhandlung liefern Felddatenanalysen einen wichtigen Beitrag zur Verhandlungsvorbereitung. Zudem können Sie als Entscheidungshilfen bei der Kalkulation von Serienersatzbedarf oder Endbevorratung herangezogen werden. Somit sind sie ein wichtiger Bestandteil des Obsoleszenz- und Ersatzteilmanagements.
Unsere Referenzen:
- Betreuung eines ganzheitlichen Zuverlässigkeitsprozesses für mehrere Baureihen (Deutscher OEM)
- Weltweite Expertenschulung Zuverlässigkeit (Deutscher OEM)
- Entwicklung, Umsetzung und operative Begleitung eines entwicklungsbegleitenden Zuverlässigkeitsprozesses (Deutscher 1st TIER)
- Internationale Schulungen Design for Reliability (Deutscher 1st TIER)
- Zuverlässigkeitszielableitung und Erprobungsplanung (zahlreiche 1st und 2nd TIER automotive, OEM und Zulieferer anderer Branchen)
- Felddatenanalyse inkl. Risikoabschätzung (zahlreiche Unternehmen sämtlicher Branchen)
- Offene Seminare Zuverlässigkeitsmanagement
Folgende Methoden werden von uns im Zuverlässigkeitsmanagement angewandt:
- Pareto-Analysen
- Schichtlinien-Diagramme
- Belastungsverteilungen (z.B. Fahrleistung, Lastzyklen, etc.)
- Weibull-Analysen
- Zuverlässigkeitsprognosen
- MTTF/MTBF-Kalkulationen
- Monte-Carlo-Simulation
- Feldsimulationen
- Kostensimulationen
Methodenportfolio:
Weibull-Analyse
Die Weibull-Analyse ist eine weit verbreitete Methode zur Beurteilung von technischen Lebensdauern und wird im Bereich der Zuverlässigkeitstechnik zur Analyse unterschiedlichster Problematiken herangezogen. Unter Verwendung der Weibull-Verteilung lassen sich die drei gängigen Ausfallverhalten
I. Frühausfälle
II. Zufallsausfälle
III. Verschleißausfälle
zielgerichtet abbilden und beschreiben.
Die Weibull-Analyse wird in der Praxis besonders zur Analyse und Bewertung von Feldreklamationen sowie zur statistischen Erprobungsabsicherung (bspw. Nachweis von Betriebsfestigkeiten) herangezogen, um anhand der Analyseergebnisse zielgerichtete Maßnahmen abzuleiten. In beiden Anwendungsfällen ist das Ziel die Beschreibung der vorliegenden Datenbasis und ggfs. die Prognostizierung zukünftiger Auftretenswahrscheinlichkeiten unter Berücksichtigung der zugehörigen statischen Konfidenz.
Industrielle Anwendungsfälle:
- Prognose zukünftiger Ausfallwahrscheinlichkeiten in der Feldbeobachtung > Ermittlung Anzahl an Schadteilen, Serienersatzbedarf, Endbevorratungsmengen, Garantie- und Kulanzkosten, …
- Statistische Erprobungsabsicherung(en) > Nutzung im Zuverlässigkeitswachstum, Auslegung Success-Run-Test, Sudden-Death-Test,…
- Ermittlung von Kennwerten aus Sicht der Betriebsfestigkeit
- Analyse lebensdauerbeeinflussender Lastmerkmale (Spannung, Zyklen, Kilometer, …)
- Ermittlung von Ausfallwahrscheinlichkeiten zu einem zugeordneten Lastzeitpunkt
- Graphische Visualisierungsmöglichkeit als Ergänzung zu nicht-parametrischen Tests (z.B. Signifikanztests)
Was wir Ihnen bieten:
Wir bieten Ihnen die erforderlichen Werkzeuge, analysieren Ihre Daten und unterstützen Sie bei der Erstellung der benötigten Auswertungen inklusive der Dokumentation(en) passend zu Ihrem Anwendungsfall – sprechen Sie uns an, wir helfen Ihnen gerne.
Zuverlässigkeitsprognose
modell (ZPM)
Viele Fragestellungen im Qualitätswesen – besonders im Warranty Management – bauen direkt auf Zuverlässigkeitsprognosen auf, so z.B. die Bestimmung der zu erwartenden Ausfälle im Feldeinsatz oder der zu erwartenden Garantiekosten. Aber auch die Ermittlung von Endbevorratungs- und Ersatzteilmengen, die Bewertung verschiedener Konzepte, Konstruktionen und Technologien über lange Einsatzzeiten sowie die Abschätzung möglicher Risiken gehören dazu. Nachfolgende Erläuterungen beziehen sich auf den Bereich Automotive, sind aber grundsätzlich auf alle Bereiche, in denen technische Produkte gefertigt und verwendet werden, übertragbar.
Erprobungsreihen, Dauerläufe und zeitraffende Tests dienen der grundsätzlichen Absicherung von Kfz-Komponenten bzgl. ihrer Funktionalität und Robustheit. Aufgrund der nur geringen Stichprobenumfänge können sie aber die oben genannten Fragen nicht beantworten, zudem auch die Korrelation zwischen Versuch und realem Feldeinsatz unbekannt ist. Dagegen spiegeln Felddaten die realen Einsatzbedingungen und alle relevanten Belastungsfaktoren wider, weshalb sie eine gute Basis zur Beschreibung des Ausfallverhaltens im Feld sind. Für größere Serienlieferungen liegen in der Regel genügend Ausfälle vor, wodurch eine gute statistische Aussagekraft gewährleistet ist. Allerdings erfolgt die vollständige Erfassung der Feldausfälle nur während der Garantiezeit, weshalb die Daten zeitlich zensiert und somit nicht vollständig sind.
…Die Zeitdifferenz zwischen Zulassung des Fahrzeuges und Ausfall der interessierenden Komponente ist nicht geeignet, um deren Belastung zu erfassen. Hierzu wäre die reine Betriebszeit notwendig, die aber in der Regel nicht erfasst wird und somit unbekannt ist. Als adäquater Ersatz hierfür kann die bis zum Ausfall gefahrene Strecke dienen, was durch umfangreiche Untersuchungen belegt ist. Allerdings ist das Fahrverhalten während der auf die Garantiezeit beschränkten Beobachtung sehr unterschiedlich (von wenigen Tausend km bis über 100 Tkm). Dies muss folglich bei Zuverlässigkeitsaussagen berücksichtigt werden.
Nachfolgend ist der Ablauf einer Zuverlässigkeitsprognose dargestellt.
Zuverlässigkeitsprognosemodelle bieten u.a. die folgenden Nutzungsmöglichkeiten:
Warranty Management
- Kalkulation von zukünftigen Garantie- und Gewährleistungskosten
- Risikomanagement bei Garantiezeiterweiterung
- Kalkulation von Serienersatzbedarf oder Endbevorratungsmengen im Ersatzteilmanagement
- Aufdeckung von Garantiebetrug
- Möglichkeit der Lieferantenbewertung/-kontrolle
- Statistische Auswertung des Zulassungsverzugs (Optimierung Supply-Chain-Management)
- Statistische Auswertung des Meldeverzugs (Optimierung Informationsfluss Zulieferer-Kunde oder intern)
Funktionale Sicherheit (ISO 26262, IEC 61508)
- Erstellung eigener Ausfallraten unter Berücksichtigung der spezifischen Belastung Ihrer Komponenten
- Möglichkeit zum Nachweis der Betriebsbewährtheit – Proven-in-Use gemäß ISO 26262
- Nachweis der Normenkonformität
Informationen Forschung & Entwicklung
- Bewertung von Systemmodifikationen
- Hilfe bei der Komponentenauswahl
- Einsatz betriebsbewährter Komponenten Optimierung der Test- und Prüfplanung (tatsächliche Belastung im Feldeinsatz)
- Feedback für Forschung und Entwicklung
Allgemeine Vorteile
- Statistische Auswertung der firmeneigenen Felddaten mittels bewährtem Modell
- Jahrelange Anwendung bei namhaften OEM und Zulieferern
- Sowohl reine Datenauswertung als auch Interpretation durch Experten möglich
- Kontinuierliche Weiterentwicklung (Stand der Wissenschaft)
Eine Zusammenfassung zum Wuppertaler Zuverlässigkeitsprognosemodell können Sie hier herunterladen:
Version Deutsch: | |
Version Deutsch-Englisch: | |
Version Englisch: |
Test- und Prüfplanung
Das Ziel der Test- und Prüfplanung ist der Nachweis, dass eine geforderte Eigenschaft über ein festgelegtes Merkmal (i.d.R. Zeit, Zyklen, Betätigungen) den Anforderungen genügt. In der Zuverlässigkeitstechnik wird hierbei meist geprüft, ob die minimal erforderliche Zuverlässigkeit (Überlebenswahrscheinlichkeit) einer Stichprobe (auch: Los, Kollektiv), die aus einer Grundgesamtheit stammt, über einen definierten Zeitraum nachgewiesen werden kann.
Die gesamten Verfahren beruhen auf der so genannten Hypothesenprüfung, bei der überprüft wird, ob die Stichprobe die Nullhypothese erfüllt. Ist dies der Fall, wird die Nullhypothese angenommen. Bei einer Ablehnung der Nullhypothese wird die Alternativhypothese angenommen.
Testverfahren
Die eigentlichen Testverfahren können sehr aufwendig und teuer werden. Daher gilt es zuerst, einen sinnvollen und damit aussagefähigen Test zu bestimmen. Denn auch ein günstiger oder schneller Test ist nutzlos, wenn die Aussagen, die anschließend getroffen werden sollen, mit den Testergebnissen abgeleitet werden können.
Nach der Bestimmung eines geeigneten Tests interessieren insbesondere die benötigte Testzeit und die auftretenden Kosten.
Im Folgenden werden einige Tests kurz mit den Testabläufen sowie den Vor- und Nachteilen beschrieben.
Success-Run-Test („Erfolgslauf“)
Bei diesem Verfahren wird die Stichprobe über einen Zeitraum getestet, um eine festgelegte Mindestzuverlässigkeit nachzuweisen. Wie der Name schon sagt, müssen alle getesteten Teile den Test ohne Ausfall „überleben“.
Ein Vorteil ist hierbei, dass der Test sehr einfach ist. Auch das Ergebnis ist eindeutig und unterliegt keiner subjektiven Bewertung, solange ein Ausfall sauber definiert ist. Des Weiteren kann, sobald das generelle Ausfallverhalten (Früh-/Verschleißausfall) bekannt ist, eine Optimierung zwischen Testdauer und Prüflingsanzahl vorgenommen werden. So gilt z.B. bei Frühausfallverhalten generell, dass eher mehr Teile getestet werden und dafür die Testzeit verkürzt werden kann. Bei Verschleißverhalten gilt der umgekehrte Sachverhalt.
Von Nachteil ist vor allem, dass über den Verlauf der Ausfallwahrscheinlichkeit keine Aussagen aufgrund der Testergebnisse möglich sind. Besonders bei einem Ausfall einer Komponente ist dies ungünstig, da nicht nur der Test negativ ausfällt, sondern darüber hinaus nur wenige zusätzliche Informationen gewonnen werden können. Insbesondere bei verschleißbehafteten Komponenten und damit langen Testzeiten kann dieser Test somit sehr nachteilig sein.
Sudden-Death-Test
Bei diesem Test wird die Stichprobe in mehrere Klassen unterteilt, die jeweils die gleiche Prüflingsanzahl aufweisen. Jede Klasse wird nun solange getestet, bis einer der Prüflinge ausfällt. Die intakten Prüflinge werden nicht weiter getestet. Anschließend wird über eine Ranggrößenverteilung das Ausfallverhalten bestimmt, da es sich bei den Ausfalldaten um einen Spezialfall einer Zensierung handelt.
Vorteilhaft bei diesem Test ist die Aufteilung in Klassen, so dass auch auf kleineren Prüfständen oftmals eine Durchführung möglich ist. Auch die Bestimmung der Ausfallfunktion ist besonders hilfreich, da somit sehr viel Wissen über die Komponenten generiert wird.
Nachteilig kann dieser Test jedoch bei Komponenten mit verschleißbehaftetem Ausfallverhalten sein, da u.U. die Testdauern in den einzelnen Klassen sehr hoch sein können. Auch der höhere Aufwand zur Testplanung wird oft als Nachteil gesehen, was jedoch häufig bei langen Testzeiten zu vernachlässigen ist.
Lebensdauertest
Bei den Lebensdauertests werden die Prüflinge über einen zuvor festgelegten Zeitraum getestet, wobei eine gewisse Anzahl an Ausfällen erlaubt ist. Die ausgefallenen Prüflinge werden nicht ersetzt. Anschließend kann mit den ermittelten Ausfallzeitpunkten und unter Festlegung eines Konfidenzintervalls die Mindestzuverlässigkeit bestimmt werden. Im Grunde ist der Success-Run-Test ein Spezialfall des Lebensdauertests.
Vorteile dieses Tests bestehen darin, dass Prüflinge ausfallen dürfen und des Weiteren eine einfache Ermittlung von Parametern der Weibull-Verteilung möglich ist, die in der Zuverlässigkeitstechnik gerne verwendet werden.
Aber auch bei diesem Verfahren besteht die Möglichkeit einer sehr langen Testdauer.vernachlässigen ist.
End-of-Life-Test (EOL)
Bei diesem Test wird das Prüflos solange getestet, bis alle Komponenten ausgefallen sind. Anschließend können die Ausfallzeiten genutzt werden, um das Ausfallverhalten zu bestimmen. Dieser Test ist ein Spezialfall des Sudden-Death-Tests, bei dem jede Klasse nur einen Prüfling hat und wird i.d.R. nur zur Robustheitsabsicherung verwendet.
Der Vorteil dieses Verfahrens gegenüber anderen ist, dass über das Ausfallverhalten der Stichprobe vollständiges Wissen vorliegt. Sinnvoll nutzbar ist dies aber nur bei einer entsprechenden Anzahl an Prüflingen.
Nachteilig ist die in der Regel sehr lange Prüfdauer.
Bei der Test- und Prüfplanung lassen sich zur Testzeitverkürzung weitere Methoden hinzufügen, wie z.B. die Laststeigerung durch Temperatur, Feuchtigkeit etc.
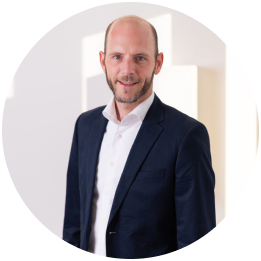
Nehmen Sie Kontakt auf!
Dirk Althaus
- +49 (0)202 – 515 616 91
- althaus@iqz-wuppertal.de